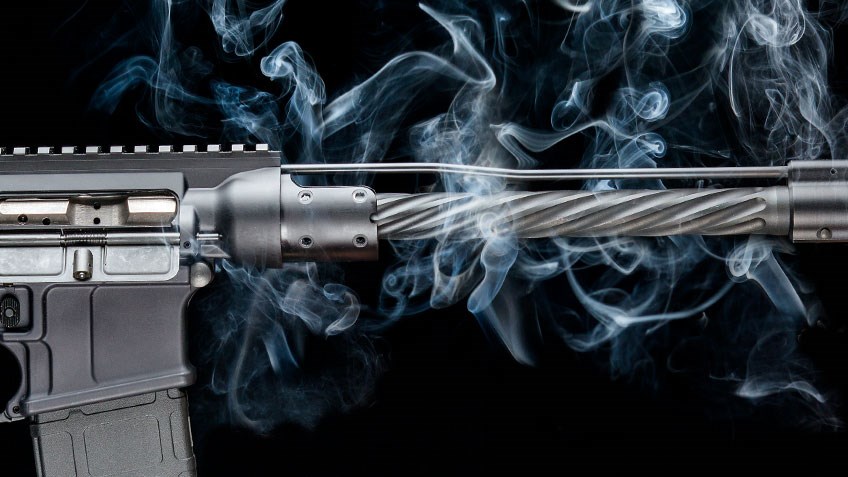
There are five barrel-rifling methods in general use: cut, button, broach, hammer forging and ECM (electrolytic cationic machining). All have their benefits. Today, we'll cover the first three methods.
1. Cut Rifling
Cut rifling is the oldest method of rifling a gun barrel. The cut-rifling method removes metal from the surface of the bore to create the grooves using a single-bladed, hook-type cutter of groove width that is pulled through the cold barrel. It is sometimes called "hook rifling" after the fishhook-shaped cutter used. Cutter depth is adjustable, so that it removes only a small amount of metalona pass. Each groove must be cut individually with multiple passes of the cutter. The cutter is indexed to each groove in turn and positively rotated by the rifling machine using a sine bar.
Advantages of cut rifling:
The shape and number of grooves and groove depth can be easily changed as necessary.
Rifling twist rate may be easily changed as required.
Rifling twist is consistent from one end to the other.
Little or no additional stress is imposed on the barrel.
Cut-rifled barrels may be contoured after rifling.
Close tolerance can be held.
Disadvantages of cut rifling:
The process is slow and not well adapted to mass production.
Cut barrels normally cost more due to the slower manufacturing process.
Some metal alloys can not be cut.
A mistake or machine malfunction at the end of the process can prove wasteful.
Cut-rifled barrels must be lapped.
Many target shooters prefer cut-rifled barrels for their uniformity and close tolerance. The cut-rifling method is normally used on prototype or test barrels where only a small number will be made for experimental purposes.
2. Button Rifling
Button rifling is a modern method that creates the grooves in the cold surface of a rifle bore by displacing metal using a bullet-shaped, super-hard button of tungsten carbide. The rifling button has the reverse pattern of the groove profile ground into its surface. As the rifling button is pushed or pulled through the barrel, the groove pattern is ironed into the bore surface by displacement. There are several variations in button-rifling procedure. Some barrelmakers prefer to pull the button through the bore, while others prefer to push it through. In most cases, the button remains free to rotate during this process, dependent on the angle of the grooves in its surface to cause the desired degree of rifling twist. As variations in rifling twist may occur during this procedure, some barrelmakers affix the rifling button to a rod and positively rotate it with a sine bar.
Advantages of button rifling:
The procedure is fast and very economical, as only a single pass of the button is required to rifle a barrel.
Button rifling is well suited to mass-production methods with high output.
Button rifling leaves a smooth, bright finish inside the barrel that need not be lapped.
Button-rifled barrels are very accurate.
Bore and groove dimensions are very consistent.
Disadvantages of button rifling:
Button rifling creates stress in a barrel; high-quality button-rifled barrels must be stress-relieved after rifling.
Buttons are expensive and difficult to make.
Different groove configurations and different rifling twists require a new button.
The button-rifling system is not flexible.
Button-rifled barrels can be extremely accurate; more bench-rest records are held by shooters using guns with button-rifled barrels than by any other type. Button-rifled barrels are very common on modern centerfire and rimfire guns.
3. Broach Rifling
Broach rifling is a modern, production-oriented variant of cut rifling that addresses some shortcomings of the cut-rifling process. While cut rifling uses a single-bladed cutter, a broach is a metal bar with sets of progressive cutting blades in its outer surface corresponding to the number of grooves. The cutting blades are fixed in spiraled succession, each blade cutting to slightly greater depth than the one in front of it. As the broach is pushed or pulled through the cold barrel, all the grooves are cut on a single pass. In some cases, a series of ever-larger broaches is run through the barrel until the desired groove depth is reached.
Advantages of broach rifling:
Fast and well-suited to mass-production methods.
Little or no stress is imposed on the barrel.
Rifling twist is consistent from one end to the other.
Broach-rifled barrels may be contoured after rifling.
Adequate tolerances can be held.
Disadvantages of broach rifling:
Broaches are expensive and hard to make.
Different groove configurations and different rifling twists require a new broach.
Broach-rifled barrels must be lapped.
The broach-rifling system is not flexible.
Match-grade barrels are not compatible with this system.
Because broach rifling was well-suited to high-volume production, it was the rifling system of choice in making military rifles during the first half of the 20th century. In the second half o the 20th century, button rifling replaced broach rifling for the manufacture of rifle barrels, with few exceptions. Today, broach rifling is commonly used to rifle some handgun barrels.
Keep an eye out for our next installment, which will cover hammer-forged rifling and ECM!
1. Cut Rifling
Cut rifling is the oldest method of rifling a gun barrel. The cut-rifling method removes metal from the surface of the bore to create the grooves using a single-bladed, hook-type cutter of groove width that is pulled through the cold barrel. It is sometimes called "hook rifling" after the fishhook-shaped cutter used. Cutter depth is adjustable, so that it removes only a small amount of metalona pass. Each groove must be cut individually with multiple passes of the cutter. The cutter is indexed to each groove in turn and positively rotated by the rifling machine using a sine bar.
Advantages of cut rifling:
The shape and number of grooves and groove depth can be easily changed as necessary.
Rifling twist rate may be easily changed as required.
Rifling twist is consistent from one end to the other.
Little or no additional stress is imposed on the barrel.
Cut-rifled barrels may be contoured after rifling.
Close tolerance can be held.
Disadvantages of cut rifling:
The process is slow and not well adapted to mass production.
Cut barrels normally cost more due to the slower manufacturing process.
Some metal alloys can not be cut.
A mistake or machine malfunction at the end of the process can prove wasteful.
Cut-rifled barrels must be lapped.
Many target shooters prefer cut-rifled barrels for their uniformity and close tolerance. The cut-rifling method is normally used on prototype or test barrels where only a small number will be made for experimental purposes.
2. Button Rifling
Button rifling is a modern method that creates the grooves in the cold surface of a rifle bore by displacing metal using a bullet-shaped, super-hard button of tungsten carbide. The rifling button has the reverse pattern of the groove profile ground into its surface. As the rifling button is pushed or pulled through the barrel, the groove pattern is ironed into the bore surface by displacement. There are several variations in button-rifling procedure. Some barrelmakers prefer to pull the button through the bore, while others prefer to push it through. In most cases, the button remains free to rotate during this process, dependent on the angle of the grooves in its surface to cause the desired degree of rifling twist. As variations in rifling twist may occur during this procedure, some barrelmakers affix the rifling button to a rod and positively rotate it with a sine bar.
Advantages of button rifling:
The procedure is fast and very economical, as only a single pass of the button is required to rifle a barrel.
Button rifling is well suited to mass-production methods with high output.
Button rifling leaves a smooth, bright finish inside the barrel that need not be lapped.
Button-rifled barrels are very accurate.
Bore and groove dimensions are very consistent.
Disadvantages of button rifling:
Button rifling creates stress in a barrel; high-quality button-rifled barrels must be stress-relieved after rifling.
Buttons are expensive and difficult to make.
Different groove configurations and different rifling twists require a new button.
The button-rifling system is not flexible.
Button-rifled barrels can be extremely accurate; more bench-rest records are held by shooters using guns with button-rifled barrels than by any other type. Button-rifled barrels are very common on modern centerfire and rimfire guns.
3. Broach Rifling
Broach rifling is a modern, production-oriented variant of cut rifling that addresses some shortcomings of the cut-rifling process. While cut rifling uses a single-bladed cutter, a broach is a metal bar with sets of progressive cutting blades in its outer surface corresponding to the number of grooves. The cutting blades are fixed in spiraled succession, each blade cutting to slightly greater depth than the one in front of it. As the broach is pushed or pulled through the cold barrel, all the grooves are cut on a single pass. In some cases, a series of ever-larger broaches is run through the barrel until the desired groove depth is reached.
Advantages of broach rifling:
Fast and well-suited to mass-production methods.
Little or no stress is imposed on the barrel.
Rifling twist is consistent from one end to the other.
Broach-rifled barrels may be contoured after rifling.
Adequate tolerances can be held.
Disadvantages of broach rifling:
Broaches are expensive and hard to make.
Different groove configurations and different rifling twists require a new broach.
Broach-rifled barrels must be lapped.
The broach-rifling system is not flexible.
Match-grade barrels are not compatible with this system.
Because broach rifling was well-suited to high-volume production, it was the rifling system of choice in making military rifles during the first half of the 20th century. In the second half o the 20th century, button rifling replaced broach rifling for the manufacture of rifle barrels, with few exceptions. Today, broach rifling is commonly used to rifle some handgun barrels.
Keep an eye out for our next installment, which will cover hammer-forged rifling and ECM!