** When you buy products through the links on our site, we may earn a commission that supports NRA's mission to protect, preserve and defend the Second Amendment. **
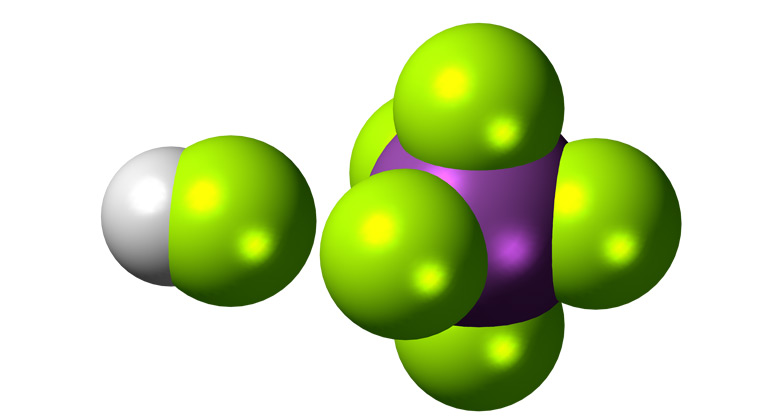
In our previous installment on rifling, we covered three methods of barrel rifling. Today, we'll talk about hammer-forged rifling and cation rifling.
Hammer forging is an ultra-modern method of rifling a gun barrel that is well suited to high-volume production by large manufacturers such as government arsenals and commercial corporations that can afford the sophisticated machinery. This method begins with a metal barrel blank about 12 inches long and 2 inches in diameter with a hole in its center honed to a fine finish. A tungsten carbide mandrel with the pattern of the rifling lands and grooves machined into its surface in reverse relief is then inserted into the hole of the blank. A forging machine with a series of radially opposed hammers is then used to compress the blank inward against the mandrel. As the hammers compress the outer surface, the blank is reduced in diameter and lengthened, simultaneously creating the bore and rifling. If needed, hammer forging can form the chamber and throat as well as a fully profiled outer surface. The spiral tracks of the hammers can often be seen on the outer surface of hammer-forged barrels. Some manufacturers turn the barrels to remove this surface, while others leave it in place.
Barrel blanks may be hammer forged cold or hot. Hot hammer forging reduces the amount of effort that the hammers must exert on the blank, and can result in better grain structure and improved strength. However, hot hammer forging is more expensive and requires more sophisticated machinery. The cold hammer-forging process produces barrels of excellent quality. Hammer-forged barrels are very common on high-volume centerfire hunting rifles and pistols where their consistency and strength outweigh their accuracy capabilities. They are not common on match-grade or varmint barrels, as their accuracy is perceived to be inferior to cut- or button-rifling methods.
Advantages of Hammer Forging:
Disadvantages of Hammer Forging:
Cation Rifling is a recently developed method of rifling a gun barrel by removing metal using acid—the cation system. In this system, the barrel blank is first drilled and reamed in a normal manner. Next, a rod with a series of groove-width wipes is pushed through the bore while being positively rotated at the desired twist rate. Each wipe deposits a groove-width trail of very strong acid that immediately begins eating into the surface of the bore. The strength and type of acid and the dwell time it is allowed to remain on the bore can be varied to obtain the desired groove depth and to suit the metallurgy. When the acid has eaten into the surface the desired amount, a neutralizing liquid is flushed through the bore to stop the acid's action. In practice, very close tolerances can be held. This system works very well on metal alloys that cannot be easily cut, buttoned or hammer forged.
Advantages of Cation Rifling:
Disadvantages of Cation Rifling:
As its advantages become better known, the cation system may become more popular, especially as it may very well be the only way new metal alloys can be rifled.
Hammer forging is an ultra-modern method of rifling a gun barrel that is well suited to high-volume production by large manufacturers such as government arsenals and commercial corporations that can afford the sophisticated machinery. This method begins with a metal barrel blank about 12 inches long and 2 inches in diameter with a hole in its center honed to a fine finish. A tungsten carbide mandrel with the pattern of the rifling lands and grooves machined into its surface in reverse relief is then inserted into the hole of the blank. A forging machine with a series of radially opposed hammers is then used to compress the blank inward against the mandrel. As the hammers compress the outer surface, the blank is reduced in diameter and lengthened, simultaneously creating the bore and rifling. If needed, hammer forging can form the chamber and throat as well as a fully profiled outer surface. The spiral tracks of the hammers can often be seen on the outer surface of hammer-forged barrels. Some manufacturers turn the barrels to remove this surface, while others leave it in place.
Barrel blanks may be hammer forged cold or hot. Hot hammer forging reduces the amount of effort that the hammers must exert on the blank, and can result in better grain structure and improved strength. However, hot hammer forging is more expensive and requires more sophisticated machinery. The cold hammer-forging process produces barrels of excellent quality. Hammer-forged barrels are very common on high-volume centerfire hunting rifles and pistols where their consistency and strength outweigh their accuracy capabilities. They are not common on match-grade or varmint barrels, as their accuracy is perceived to be inferior to cut- or button-rifling methods.
Advantages of Hammer Forging:
- Hammer forging consistently produces high-quality barrels.
- It can form chamber, throat and outer profile if necessary.
- It does not remove metal; there's no waste or chips.
- It produces barrels with excellent grain structure and high strength.
- Hammer forging produces superb bore finish, no lapping needed.
Disadvantages of Hammer Forging:
- Machinery and mandrels are expensive.
- It's inflexible; changes in rifling require a new mandrel.
- Quality is very good, but not match grade.
- Hammer tracks are left on outer surface.
- Process introduces stress in the barrel; must be stress-relieved.
Cation Rifling is a recently developed method of rifling a gun barrel by removing metal using acid—the cation system. In this system, the barrel blank is first drilled and reamed in a normal manner. Next, a rod with a series of groove-width wipes is pushed through the bore while being positively rotated at the desired twist rate. Each wipe deposits a groove-width trail of very strong acid that immediately begins eating into the surface of the bore. The strength and type of acid and the dwell time it is allowed to remain on the bore can be varied to obtain the desired groove depth and to suit the metallurgy. When the acid has eaten into the surface the desired amount, a neutralizing liquid is flushed through the bore to stop the acid's action. In practice, very close tolerances can be held. This system works very well on metal alloys that cannot be easily cut, buttoned or hammer forged.
Advantages of Cation Rifling:
- Uses no cutters, no buttons and no mandrels.
- Flexible system that can easily vary size and number of grooves and twist rate.
- Produces excellent bore finish.
- Does not impose stress on the barrel.
- Will rifle hard or exotic metal alloys that cannot be rifled by other methods.
Disadvantages of Cation Rifling:
- Equipment is expensive.
- Requires storage and handling of strong acids and neutralizers.
- System not yet well known.
As its advantages become better known, the cation system may become more popular, especially as it may very well be the only way new metal alloys can be rifled.