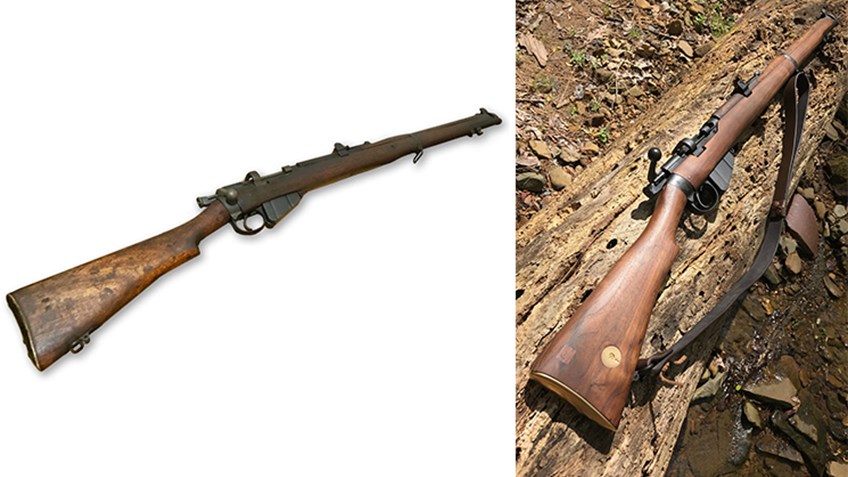
Browning and bluing are terms used to describe any of several chemical treatments of metals that are essentially controlled rusting processes. On ferrous metals, bluing appears as a dark-colored, protective oxide layer on the surface.
Probably the earliest surface treatment for metals was browning. The procedure was popular with early gunsmiths, and by 1700 the process was understood and used by most. The process was understood and used by most. The process begins by dissolving ordinary table salt in distilled water. The parts to be browned are cleaned, polished and thoroughly degreased. If a gun barrel was being browned, the bore was liberally coated with grease and plugged at both ends with tapered wooden dowels. Next, the saltwater solution was liberally applied to the surfaces to be browned, and the parts left to stand in a humid environment. Within 12 hours or so a thin coat of rust formed. The parts would be lightly rubbed with degreased, fine steel wool to remove the loose rust, leaving a slightly colored surface. The parts were then recoated and returned to the humid environment to allow further rusting. The cycle of rusting/rubbing-rusting/rubbing was repeated until the desired shade of brown was achieved.
Cold rust bluing is a similar process. A solution of hydrochloric and nitric acids diluted in distilled water with a small quantity of iron filings added is prepared. As with browning, the parts to be blued are polished and degreased, the exposed surfaces swabbed with the bluing solution, and the part left to stand in a humid location. After 12 hours, the loose rust is rubbed off with degreased steel wool or a stainless steel wire brush, the surface is recoated with bluing solution and the part is returned to its humid environment. The process is repeated until a deep blue finish is achieved—which may take from five to 10 days. Although a very slow process, cold rust bluing produces a deep blue color generally considered to be the most durable kind of bluing. Like browning, it can be used on side-by-side or over/under shotguns with barrels joined by soft solder, which would be corroded by hot bluing solutions.
By contrast, hot-water bluing processes can produce a deep blue finish in just a couple of hours, rather than several days. Hot-water bluing uses a bluing solution containing potassium nitrate, sodium nitrate, potassium chlorate and mercury bichloride that is applied by hand to a clean steel surface that has been heated by immersion in boiling water. After applying the bluing solution, the part is immersed in the boiling water for five minutes, then re-coated with bluing solution. This cycle is repeated, with loose rust being rubbed off with degreased 0000 steel wool, until a rich blue-black color is achieved.
Hot caustic bluing is a fast metal-treatment process suited to high volumes. Consequently, it has become the preferred method for bluing by most gun manufacturers today. In this process, the clean metal parts are immersed in a solution of sodium hydroxide salts heated to about 300 degrees Fahrenheit. Midway through the immersion period, the parts are removed from the bluing tank, rapidly chilled in cold water, then reimmersed in the salts to promote a a deeper final color. Finally, the blued parts are removed from the salt solution, washed in boiling water to remove all traces of salt, and coated with water-displacing oil. Hot caustic bluing cannot be used on non-ferrous metals, such as aluminum, magnesium and zinc, as they will dissolve and contaminate the bluing salts.
Heat bluing is a process often used for finishing small parts, such as pins, screws, triggers and hammers. In this method, the parts are heated to 600-700 degrees Fahrenheit in a propane flame or burning charcoal, then immersed in oil. A variant of this process involves heating the part in a bath of molten potassium nitrate, then dipping the parts in water. Heat bluing produces an attractive deep-blue finish, depending upon the heat and the metallurgy of the part. However, this process is not suitable for large parts due to the difficulty of producing an even shade of blue throughout.
Cold-bluing solutions usually work through the chemical actio of selenium. The finish produced is not as durable as other blued finishes. For this reason, cold blues are not suited for bluing large parts or entire guns. However, cold blues excel for touch-up work to hide nicks, scratches and blemishes in existing blue finishes, although they may not match the existing bluing perfectly.
Do note that stainless steel is impervious to most bluing solutions, including instant bluing products.
Probably the earliest surface treatment for metals was browning. The procedure was popular with early gunsmiths, and by 1700 the process was understood and used by most. The process was understood and used by most. The process begins by dissolving ordinary table salt in distilled water. The parts to be browned are cleaned, polished and thoroughly degreased. If a gun barrel was being browned, the bore was liberally coated with grease and plugged at both ends with tapered wooden dowels. Next, the saltwater solution was liberally applied to the surfaces to be browned, and the parts left to stand in a humid environment. Within 12 hours or so a thin coat of rust formed. The parts would be lightly rubbed with degreased, fine steel wool to remove the loose rust, leaving a slightly colored surface. The parts were then recoated and returned to the humid environment to allow further rusting. The cycle of rusting/rubbing-rusting/rubbing was repeated until the desired shade of brown was achieved.
Cold rust bluing is a similar process. A solution of hydrochloric and nitric acids diluted in distilled water with a small quantity of iron filings added is prepared. As with browning, the parts to be blued are polished and degreased, the exposed surfaces swabbed with the bluing solution, and the part left to stand in a humid location. After 12 hours, the loose rust is rubbed off with degreased steel wool or a stainless steel wire brush, the surface is recoated with bluing solution and the part is returned to its humid environment. The process is repeated until a deep blue finish is achieved—which may take from five to 10 days. Although a very slow process, cold rust bluing produces a deep blue color generally considered to be the most durable kind of bluing. Like browning, it can be used on side-by-side or over/under shotguns with barrels joined by soft solder, which would be corroded by hot bluing solutions.
By contrast, hot-water bluing processes can produce a deep blue finish in just a couple of hours, rather than several days. Hot-water bluing uses a bluing solution containing potassium nitrate, sodium nitrate, potassium chlorate and mercury bichloride that is applied by hand to a clean steel surface that has been heated by immersion in boiling water. After applying the bluing solution, the part is immersed in the boiling water for five minutes, then re-coated with bluing solution. This cycle is repeated, with loose rust being rubbed off with degreased 0000 steel wool, until a rich blue-black color is achieved.
Hot caustic bluing is a fast metal-treatment process suited to high volumes. Consequently, it has become the preferred method for bluing by most gun manufacturers today. In this process, the clean metal parts are immersed in a solution of sodium hydroxide salts heated to about 300 degrees Fahrenheit. Midway through the immersion period, the parts are removed from the bluing tank, rapidly chilled in cold water, then reimmersed in the salts to promote a a deeper final color. Finally, the blued parts are removed from the salt solution, washed in boiling water to remove all traces of salt, and coated with water-displacing oil. Hot caustic bluing cannot be used on non-ferrous metals, such as aluminum, magnesium and zinc, as they will dissolve and contaminate the bluing salts.
Heat bluing is a process often used for finishing small parts, such as pins, screws, triggers and hammers. In this method, the parts are heated to 600-700 degrees Fahrenheit in a propane flame or burning charcoal, then immersed in oil. A variant of this process involves heating the part in a bath of molten potassium nitrate, then dipping the parts in water. Heat bluing produces an attractive deep-blue finish, depending upon the heat and the metallurgy of the part. However, this process is not suitable for large parts due to the difficulty of producing an even shade of blue throughout.
Cold-bluing solutions usually work through the chemical actio of selenium. The finish produced is not as durable as other blued finishes. For this reason, cold blues are not suited for bluing large parts or entire guns. However, cold blues excel for touch-up work to hide nicks, scratches and blemishes in existing blue finishes, although they may not match the existing bluing perfectly.
Do note that stainless steel is impervious to most bluing solutions, including instant bluing products.