** When you buy products through the links on our site, we may earn a commission that supports NRA's mission to protect, preserve and defend the Second Amendment. **
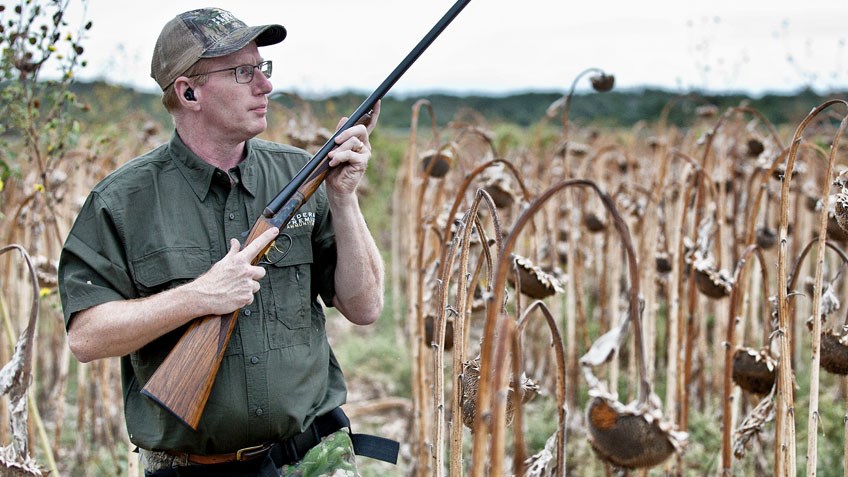
Modern smoothbore shotgun barrels are usually made in one of three ways: By drilling and reaming seamless steel tubing; by drilling and reaming steel bar stock; and by hot or cold hammer forging. Some shotgun bores are tapered from forcing cone to muzzle, often in several distinct stages. Immediately in front of the chamber is the forcing cone that centers the shot charge or slug in the bore. The American practice is to make forcing cones relatively short with a steep angle, while European practice favors longer forcing cones with shallower angles. Many European shotguns have chrome-lined bores and chambers.
While the bores of smoothbore shotgun barrels may be polished, they are not lapped or air-gauged. Although straightness and bore uniformity of shotgun barrels remain important, shotgun barrels do not require the same level of precision and uniformity as rifle barrels.
Rifled shotgun barrels designed exclusively for slug use are manufactured in a manner similar to rifle barrels, although they are rarely lapped. While all rifle barrels in a given caliber will have standardized bore and groove diameters, bore dimensions and rifling twist rates for rifled slug barrels are not yet standardized. Consequently, accuracy and velocity with slugs in such barrels may vary markedly among different gun brands.
As most pump and semi-automatic shotguns have a non-stressed receiver, the barrel can be quickly and easily removed for exchange, maintenance or travel. In such shotguns, the bolt locks into a notch or recess cut into a thick-walled extension on the back end of the barrel. This allows the use of aluminum alloy receiver with no loss of strength or safety.
Today, barrels for break-action shotguns (whether side-by-side, over/under or single-barrel models), are mostly built on the monobloc principle. In this type of construction, the barrels are silver-soldered into a machined steel monobloc assembly containing the ejector cuts and the solid projections under the breech end (called lumps) that fit into the action. These projections are engaged by the locking mechanism to hold the action shut. Monobloc construction is a simpler and easier mounting system than the old method of producing barrels with forged integral lumps.
While the bores of smoothbore shotgun barrels may be polished, they are not lapped or air-gauged. Although straightness and bore uniformity of shotgun barrels remain important, shotgun barrels do not require the same level of precision and uniformity as rifle barrels.
Rifled shotgun barrels designed exclusively for slug use are manufactured in a manner similar to rifle barrels, although they are rarely lapped. While all rifle barrels in a given caliber will have standardized bore and groove diameters, bore dimensions and rifling twist rates for rifled slug barrels are not yet standardized. Consequently, accuracy and velocity with slugs in such barrels may vary markedly among different gun brands.
As most pump and semi-automatic shotguns have a non-stressed receiver, the barrel can be quickly and easily removed for exchange, maintenance or travel. In such shotguns, the bolt locks into a notch or recess cut into a thick-walled extension on the back end of the barrel. This allows the use of aluminum alloy receiver with no loss of strength or safety.
Today, barrels for break-action shotguns (whether side-by-side, over/under or single-barrel models), are mostly built on the monobloc principle. In this type of construction, the barrels are silver-soldered into a machined steel monobloc assembly containing the ejector cuts and the solid projections under the breech end (called lumps) that fit into the action. These projections are engaged by the locking mechanism to hold the action shut. Monobloc construction is a simpler and easier mounting system than the old method of producing barrels with forged integral lumps.